A radiant and very smooth surface
Electropolishing can be chosen for both functional and decorative applications. For decorative, complex applications, brightness can be achieved that cannot be matched with any other process. The resulting smooth and chromium-enriched surface with a very low Ra value, which is free from impurities, has an optimum corrosion resistance, also in critical applications, where the material is less sensitive to dirt adhesion and is easy to clean.
The most important applications are found in the food and pharmaceutical industry or clean room environments.
The advantages of electropolishing are:
- Reduction of surface roughness (circa 50% in Ra;
- Removal of sharp edges (burrs, corners), sometimes referred to as chemical milling;
- Results in a bright, reflecting surface, with removal of light scratches and a cosmetically desirable product with increased light reflection;
- Improved resistance to corrosion due to chromium enrichment of the surface;
- Reduced dirt adhesion;
- Surface is easier to clean;
- Reduced friction;
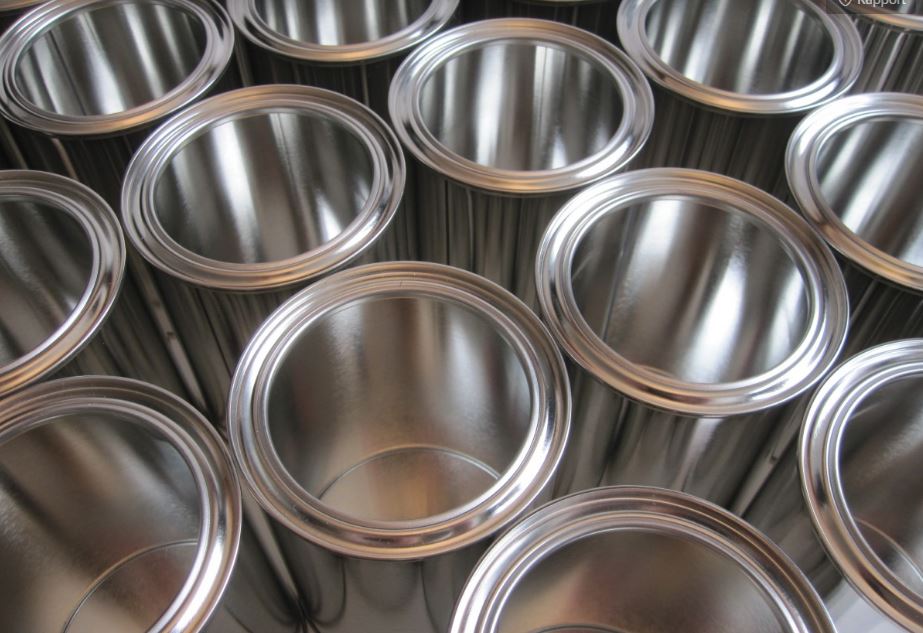
The electropolishing process
Electropolishing is applied commercially on stainless steel including duplex and hastelloy. In practice, it is a process similar to electroplating, with the difference that no coating is applied, but that material is removed from the surface. Just like with electroplating, the component is immersed in an electrolyte and a direct current. Electroplating is a cathodic process while electropolishing is an anodic process. The component is connected to the anode (positive). The cathode (negative) consists of a suitable conductor. After the component and the cathode have been immersed in the electrolyte (a conductive liquid), the electrical circuit is closed and a direct current is applied. Special counter electrodes (jigging) are designed to electropolish parts with complex shapes.
Applications for electropolishing
The most important applications are found in the food and pharmaceutical industry or clean room environments; parts such as barrels, reactors, autoclave bins, baskets, filtration and catering supplies, where very high demands are made on cleanliness. Electropolishing gives stainless steel considerably less dirt adhesion than any other method of surface treatment. Increased cleanability ensures both a short stop during plant maintenance and a high cleanliness of the product.